Liners or linings for Polywear
We manufacture Polywear® linings, these can be composite (rubber bonded to other materials) or only rubber. They are designed in a personalized way according to the needs that each operation faces.
Our experience of more than 35,000 manufactured liners allows us to develop the most appropriate engineering based on the objective, with the best costs and production times. This allows us to propose designs that improve mill productivity through metallurgical studies: angle of attack, packing area, dissipated energy and collision rate, etc.
Our technical proposals are made based on the operating conditions of each mill, after a campaign they are contrasted with reality to quantify the real benefits and validate our promise, the ultimate goal is always to reduce costs per processed ton.
POLYWEAR
- Useful life +50%
- Stop reduction -50%
- Weight reduction -50%
- Tonnage increase +10%
- Energy saving -7%
- P80 reduction (balls) -10%
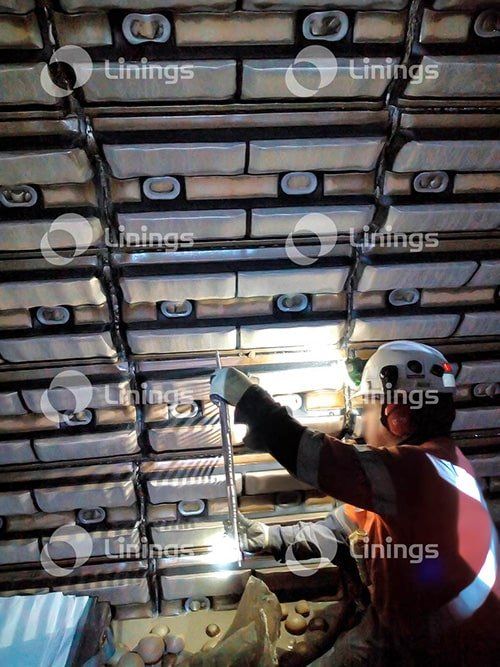
Linings for ball mills
In the case of ball mills, we make rubber or composite mill liners for the caps and cylinder. In lids the designs can be flat bar or mono block and in the cylinder the liners can be mono wave, flat bar, double wave (being the first to launch them on the market) as well as double-double wave.
In a ball mill, grinding is by attrition and compression. Our approach through a metallurgy study is to optimize grinding. Our liners grind from the start, without having to place more balls, and all the way through, without having to increase speed. If a composite mill liner is not designed properly, the grinding will be impaired, having to compensate by placing a higher percentage of balls.
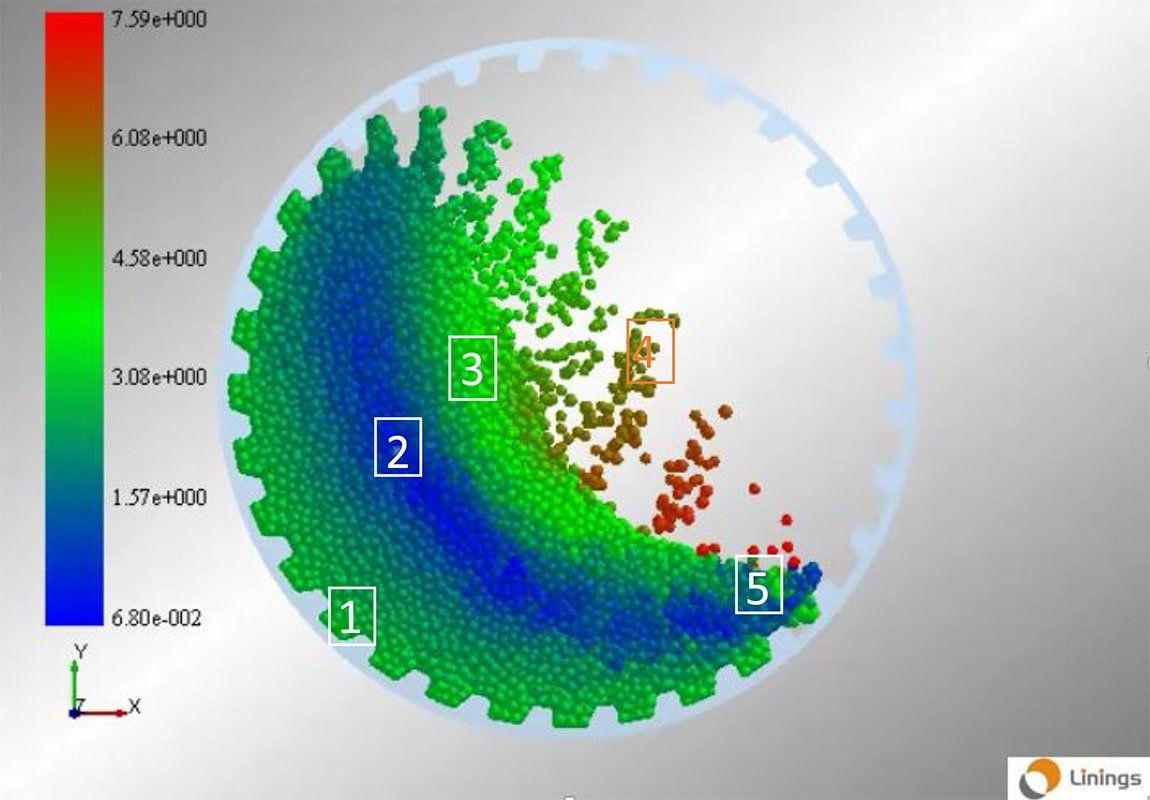
Legend
- Grinding zone by attrition and compression.
- Dead zone.
- Zone with the greatest amount of grinding by attrition.
- The balls have a high impact capacity.
- Ball impact zone on the foot of the kidney.
Grinding Simulation
SAG Mill Liners
We manufacture composite POLYWEAR linings for SAG mills: Outer (patented), deflectors and inners. We achieve a custom combination of abrasion and impact resistant metals, bonding them with highly durable one-piece rubber which in turn achieves significant energy savings and faster installation and removal times. We have made liners for up to a 36 foot SAG mill.
Our continuous improvement processes ensure that each campaign is better than the previous one, the constant feedback from users ensures that teamwork is a fundamental factor to achieve new challenges. All our composite or rubber linings have the corresponding caps protecting the fastening, in order to extend its life span, thus avoiding premature wear. The fastening can be placed with internal or external bolting at the request of the user.